Categories
- Wire & Cable
- Multi-conductor & Signal Cable
- Battery Cable Assemblies
- Terminals and Connectors
- Electrical Parts
- Electrical Tools
- ID Products
- Wire Management
- Tape & Sealant
- Mounting Panels & Panel Blanks
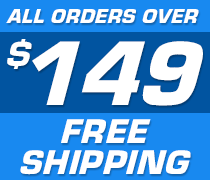
Need Help?
Click HereGet a Business Account
Apply HereWire Joints
What are Wire Joints?
Wire joints refer to electrical wire connectors or methods that are used to connect two or more wires together. This can include things such as butt splices, closed end connectors or other electrical connector types. If you are looking for butt splices, we have a dedicated section for them HERE. Each style of wire joint we carry has a set range of wire sizes it will accept. For example, we carry heat shrink closed end connectors 22 AWG – 16 AWG. This specific type of wire connectors are made to handle either four 22 AWG wires or two 16 AWG wires. It could even handle two 22 AWG wires and one 16 AWG wire. It is important to know which size is right for your project since our closed end connectors can connect between two to four wires of different sizes.
"It is important to know which size is right for your project since our closed end connectors can connect between two to four wires of different sizes."
Where are wire joints implemented?
Wire Joints can be used in multiple ways that other terminals cannot
Wire joints are implemented in various industries where wires need to be combined or terminated. They are ideal for multiple uses which makes them perfectly suited for use in new installations as well as when replacing parts. When considering the types of crimp connectors to use, pay attention to the current condition of your electrical system. If you are dealing with faded connectors, damaged wires, or damaged connectors, then wire joints may just be the perfect solution for you. All you will need are the proper tools and wires. Now that we have that out of the way, let us talk about how you might use them?
How do I use wire joints?
Wire joints are surprisingly simple to use given that you have the correct tools on hand. Let us say you plan to use the 22 AWG to 16 AWG closed end connectors with four 22 AWG wires that need to be connected. You would start by prepping your four wires, stripping them to the correct length. Once they are properly stripped, you would line them up and insert all four into the open part of the closed end connector until the insulation of the wire butts up to the barrel of the connector. With all four wires inserted, you would next crimp them with the appropriate crimping tool. Once the crimp is in place, you would apply heat to the outer heat shrink until it constricts and fully encapsulates the wire ends. That is it. Now you have created an environmentally sealed connection point.
Wire joints can also be used as splices, wire butts, parallels, or even dead-end caps. This makes them an even more useful connector to use since they have multiple applications.
What advantages do they offer?
Wire joints are crimp connectors that offer advantages that you may not find with other connectors. For starters, they are advantageous in environments where corrosion is an issue. The epoxy lined heat shrink we talked about earlier helps to protect the wires from exposure to elements such as moisture. Wire joints are also a safer alternative to wire nuts. The seal they make reduces the risk of electric shock that may occur with other types of connectors. Another advantage is their quick install time. Wire joints can be installed in a matter of minutes and last for years. Now that we've taken a look at some of the advantages of wire joints, let us take a look at where you might use them.
Moisture
Shock Protection
Saves Time
Where would I use wire joints?
Wire joints are electrical connectors that are useful anywhere you have electrical wires that need to be spliced or end capped. They are utilized by a wide range of industries due to their ease of installation, cost-effectiveness, high level of circuit protection, and multiple application usage. They are found in just about any industry that deals with electrical connections. You will want to use wire joints anywhere you have a splice or dead-end that needs protection from environmental hazards. This is just another one of the advantages that come with wire joints.
What types of wire joints are available?
Pacer offers a range of wire joints so that you can find the best suited option. We offer crimpable closed-end connectors as well as heat shrink connectors of various sizes. Each of these wire joints is designed for specific applications. Take a look at the chart below to see the differences between each style.
Image | Wire Joint Type | Gauge Sizes | Colored Dash |
---|---|---|---|
![]() |
Crimpable Closed End Connectors | 6AWG | N/A |
![]() |
Heat Shrink Connectors - Closed End | 18 AWG - 12 AWG | Yellow |
![]() |
Heat Shrink Connectors - Closed End | 22 AWG - 16 AWG | Blue |
What environmental protection do they offer?
Since our wire joints carry heat shrink insulation, they are resistant to moisture, oil, abrasion, corrosion, and impact. When the epoxy-lined heat shrink has been properly activated, it creates a waterproof seal making these wire joints ideal for use in environments where exposure to the elements is an issue.
Moisture
Oil
Abrasion
Corrosion
Impact
Given that these connectors deal with multiple wires of various sizes, it can be somewhat confusing as to which one is best suited for your project. Contact a Pacer expert today and let us help you choose the right wire joint.